Your Comprehensive Guide to Metal Wax Seals
- waxseals4you
- Sep 20, 2021
- 2 min read
Casting is one of the earliest known forms of metalworking. In its most basic form, the best antique wax seals involve heating the metal until it melts and then casting it into a mold. As the metal cools, it forms a mold. Early castings were crude with numerous surface anomalies, which required a lot of machine work to achieve the desired quality of surface texture. Modern casting technology produces very good tolerances and requires little or no finishing work for casting.
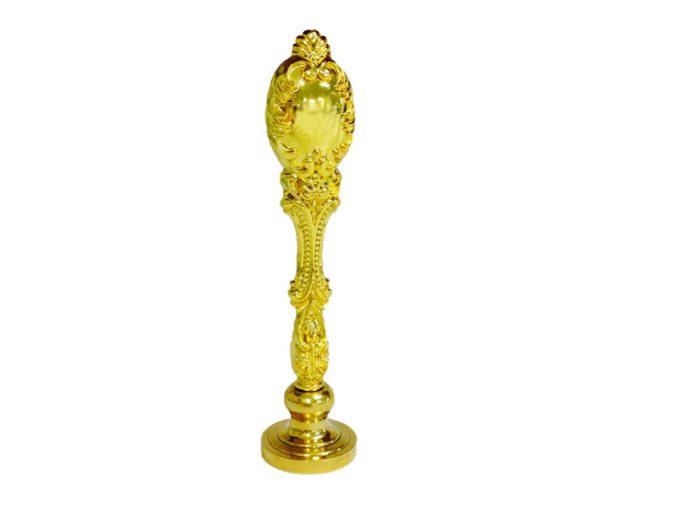
The artist making the perfectly designed antique and metal wax seals should be both a foundry man and an artist. Bronze is one of the earliest known alloys for man and is made of tin and copper. Being pale, it becomes a low viscosity liquid when it melts and thus it has the ability to fill even small cracks in the mold, allowing the casting to be produced with excellent details. Although bronze castings are the most common, almost any metal can be cast. The artist needs to know what kind of mold to use with which metal. And he needs to know how the metal melts.

How to cast metal wax seals?
The casting process begins with the production of the mold. The most common type is called the lost wax casting method. Being easy to create and with the ability to create molds with tiny details, it is a favorite of artists. The first artist makes a wax sculpture. This statue is then used to make the mold. Molds can be made from a variety of materials, from sand to latex, depending on the amount of detail required. Latex is used when very fine details are involved as it creates a skin-like coating on the sculpture and removes even the smallest details. The idol is then removed from the mold.
The molten wax is poured into the mold until the required thickness is obtained and then the wax copy is removed and any imperfections on the surface are removed. A shell is then formed around the copy using a mixture of sand and liquid silica. The shell is heated until the wax melts and the drain in the shell comes out of the holes.

Then the final mold is ready and molten metal is poured into it. After it has cooled and taken the shape of a mold, the shell is removed and the finished molding is available. The cast then removes the imperfections on the casting and makes it smooth, then it is coated to give it the desired finish.
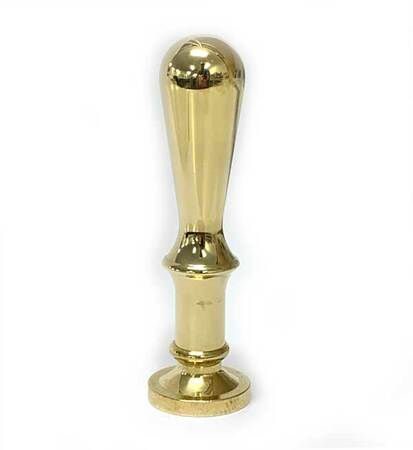
The metal art foundry can be of any size, from a small piece of gold jewelry to a huge cast sculpture that can fit indoors. The advantage of this type of metal art is the exquisite details that can be produced.
Modern metal smelting techniques ensure that the molten metal entering the mold is flawless and free to hold diamonds (in the case of jewelry) or hardness of nature (in the case of garden sculptures). Strong enough to survive. In addition, once the mold is made, multiple copies of the work of art can be made.
Contact Seals4You.
Comentários